100% 클린-컷 - 파인블랭킹(Fineblanking), 자체 표준 수립
파인블랭킹(Fineblanking)은 기본적인 제품뿐 아니라 설계가 복잡한 제품 계열을 생산하려는 여러 사용자들에게 효율적인 비용과 정밀도 높은 제품을 제공할 수 있다. 파인블랭킹은 progressive 나 transfer 기능 등을 이용하는 새로운 기술적 접근 방식을 제시하고 있으며, 이는 전체적인 비용절감에 도움을 준다. 부품의 형상 및 복잡성에 따라 개별적으로 개발 및 적용되는 금형 기술은 다운스트림 동작 수를 줄여준다.
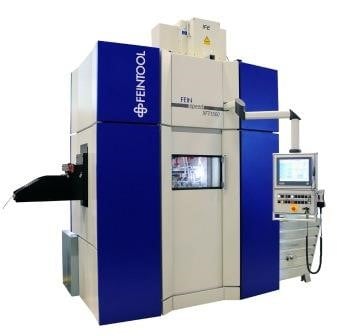
파인블랭킹(Fineblanking)은 최고 약 15mm의 소재를 커팅하기 위한 공정이다. 이 공정의 가장 큰 장점은 티어 오프나 크랙 없이 클린 컷 표면의 제품을 생산할 수 있으며, 추가적인 후공정도 상당부분 필요하지 않는 것이다. 기본적인 블랭크 공정은 제품 표면의 3분의 1정도의 클린 컷이 가능했으며, 나머지는 티어 오프 되곤 했다. 반면에 파인블랭킹 공정은 소재 두께의 100%까지 표면을 클린 컷 할 수 있다. 파인블랭킹 프레스와 금형 한 벌이면 복잡한 제품도 안정적인 반복 정확성과 경제적인 가격으로 분당 최고 200 스트로크의 속도로 생산 가능하다.
파인블랭킹의 트리플 액션(Force)은 제품의 품질 및 성능에 결정적인 영향을 미친다. 공정 초반의 액티브 포스(Active Force)는 비링(Vee-Ring) 포스 및 카운터 포스이다. 비링 포스는 소재에 톱니 식 비링으로 압력을 가하고, 카운터 포스는 박판 금속 스트립(Sheet Metal Strip)을 펀치에 대고 누른다. 블랭킹 공정이 시작되기도 전에, 이 소재는 둘러 막힌 시어(Shear) 주변부의 양 측면이 단단하게 고정된다. 그런 다음 3번째 포스, 블랭킹 포스가 가해지면서 고정되어 있는 부품을 커팅한다.
오늘날 파인툴(Feintool)은 파인블랭킹 기술 분야의 선도주자로, 파인블랭킹 프레스 및 주변기기에서 금형에 이르기까지 파인블랭킹 공정 전반과 단일 공급원으로 전체 시스템을 공급할 수 있는 전세계에서 유일한 기업이다. 부품 설계 및 시제품 제작, 엔지니어링, 금형 설계 또한 주력 분야들이다.
뛰어난 커팅 품질
제품 소재의 성형성과 금형의 커팅 엘리먼트 등의 두께 및 최대 부하는 일반적인 제품 커팅의 가능성 제한할 수 있다. 하지만 금형 소재의 발전과 파인툴의 공정 설계기술은 제한적이었던 파인블랭킹 분야를 점점 더 넓혀 나가고 있다. 정밀한 조임톱날을 갖춘 자동차 시트 조정기 부품은 하나의 최신 사례이다. 이 톱니의 사이즈는 3mm ~ 6mm의 소재 두께에 적합한 0.3 ~ 0.5의 모듈 사이즈와 거의 근사치로 동일하다.
뛰어난 생산량
높은 장비의 가동율과 서보 프레스의 개발로 인한 장비 스트로크 극대화로 생산량 측면에서도 많은 발전이 이뤄졌다. 자동차 도어락 제품 제조업체의 사례를 들 수 있는데, 전체 450톤 포스를 이용하는 단일 스트로크에서 4개의 플런저(Plunger) 블록은 평균 분당 100스트로크 사이클 속도로 소재 스트립에서 동시에 커팅이 가능하다.
복잡한 제품의 증가
제품의 다양성과 설계의 복잡성으로 인해 3D 시뮬레이션을 이용한 제품 개발이 최근에 집중되고 있다. 이는 효율적인 힘의 사용과 기존의 형상을 이용 또는 변형을 함으로써 프레스의 효율적인 사용이 가능하다. 또한 복잡한 제품이 증가 함으로써 프로그레시브나 트랜스퍼 금형 같이 다기능의 금형도 개발되고 있다.
다운스트림 동작 통합
메인 프로세스에 다운스트림 동작 통합에 관한 유사한 패턴이 부상하고 있다. 대표적인 사례는 파인블랭킹(버링(Burring) 포함)과 그 다음의 플랫 부품의 디버링(Deburring)이 통합되고, 벤딩 프로세스가 이어진다는 점이다. 여러 프로세싱 단계를 하나의 금형으로 통합함으로써 부품을 더욱 빠르고, 더욱 경제적으로 생산할 수 있게 되었다. 또한 리그라인드까지 금형의 서비스 수명을 획기적으로 늘릴 수 있다.
소재 사용량 감소
소재는 간혹 부품당 유닛 단가의 50% 이상을 차지하기도 한다. 따라서 파인블랭크 윤곽선의 외부 스크랩 브리지 폭과 골격 스트립의 보조 기능에 필요한 공간은 가능한 한 최대한 줄여야 한다. 성공의 핵심은 계획 단계의 초반에서 찾을 수 있다. 최상의 결과는 소재를 절감함으로써 비용을 줄이는 것으로, 제품 디자인과 소재 및 금형 설계 간의 상호작용을 초기에 고려해야만 달성할 수 있다.
이미지 1: 기존의 블랭킹과 파인블랭킹과의 차이: 전통적인 블랭킹 부품은 표면의 3분의 1 정도만 클린-컷이 되고 나머지는 티어-오프 상태가 된다. 반면 파인블랭킹의 경우 전체 표면의 최고 100%의 소재 두께까지 클린-컷이 된다.
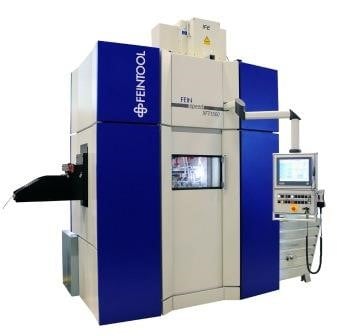
이미지 2: 서보 모터 파인블랭킹 프레스 XFT1500speed를 통해 파인툴은 또 다른 이정표를 달성했다. 최초로 이 파인블랭킹 프레스는 최고 분당 200 스트로크를 수행한다.
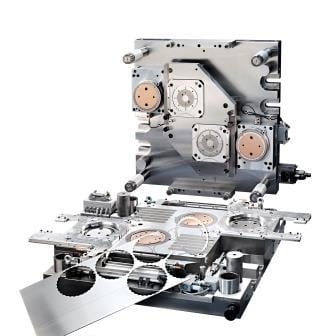
이미지 3: 금형 소재 및 블랭킹 프로세스에 대한 탁월한 아이디어가 업계에서 지속적으로 개발되면서 파인블랭킹의 범주를 획기적으로 넓혀 나가고 있다.
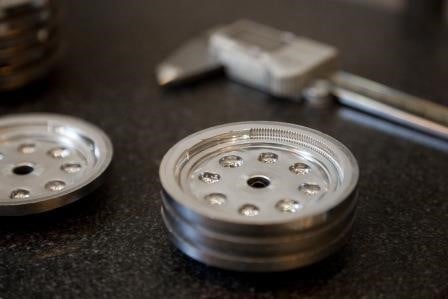
이미지 4: 정밀한 조임 톱날을 갖춘 자동차 시트 조정기 부품